From the quality of corrugated board, we can see the production strength of an enterprise. As the first production process of corrugated box, the corrugated board production line plays a key role in the cost and quality of the products. It is also the most variable and the most difficult link to control in all production processes. Only by systematically solving the five factors of good people, machine, material, method and environment, can we effectively reduce the production of waste products in the corrugated board production line and produce high-quality products.
People are the most critical factor and the most unstable factor. Two aspects are emphasized here: team spirit and personal operation skills of corrugated board production line operators.
Corrugated board production line is a production line integrating steam, electricity, hydraulic pressure, gas and machinery. It involves several key processes, such as single-sided machine, conveying bridge, gluing compound, drying, pressing line and vertical and horizontal cutting. If any link is not well coordinated, the operation of the whole production line will be affected. Therefore, the operators of corrugated board production line must have a strong sense of team work And the spirit of collaboration.
At present, most of the operation and technical personnel of corrugated board production line in the enterprise are slowly groping and growing up in the production of the enterprise. They work with production experience, lack of professional operation skills training and learning, and are not proficient in the driving ability of the equipment, and lack of prediction and Prevention of potential problems. Therefore, enterprises should first pay attention to the skills training of corrugated board production line personnel and the training of corrugated box related basic knowledge. They should not hesitate to invite people to or send them out for learning. Moreover, they should pay attention to personnel training, establish enterprise culture with their own characteristics, attract high-level technical talents of corrugated board production line, and make enterprises have strong cohesive force and personnel tools Have a high sense of identity.
Stable operation of equipment is the basis of quality assurance of corrugated board. In this regard, enterprises should carry out their work from the following perspectives.
The abnormal shutdown of corrugated board production line will produce a lot of waste products, which will reduce the production efficiency and increase the production cost. The maintenance of equipment is the most effective way to reduce the downtime rate.
The normal operation of the equipment largely depends on whether the daily maintenance work can keep up with. The general equipment maintenance principles are: sufficient lubrication, clean and complete, careful and meticulous.
There are hundreds of lubricating parts in corrugated board production line. According to different lubricants used, they can be divided into oil lubrication part and grease lubrication part. The corresponding lubricant should be strictly used for different lubricating parts, and the lubricating parts should be fully lubricated. If the temperature of corrugated roller and pressure roller is high, high temperature grease should be used strictly.
The cleaning work of the equipment also plays an important role in the maintenance process. It is closely related to the lubrication condition of the equipment. It should be free of dust and debris to avoid accelerated wear and even damage of parts due to the influence of dust and debris.
Make detailed maintenance plan according to the equipment maintenance process.
Real time monitoring is very necessary for the management of vulnerable parts of equipment. Enterprises should establish a tracking account for the use of vulnerable parts of equipment, conduct real-time monitoring and analysis, find out the causes of rapid wear of vulnerable parts, and formulate countermeasures, so as to prevent in advance and avoid unplanned shutdown due to damage of vulnerable parts.
In general, the management of vulnerable parts should take the following two measures: one is to change the material and manufacturing process of vulnerable parts to achieve the purpose of extending the service life; the other is to use in a reasonable environment to reduce unnecessary damage caused by human and environmental factors.
In recent years, the technical innovation of corrugated board production line emerges in an endless stream, and new technology highlights lead enterprises to start the renovation of key components of corrugated board production line equipment.
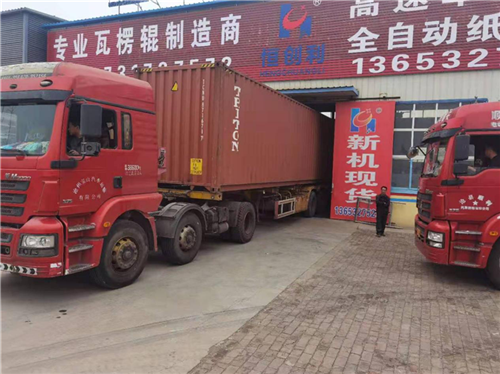
Using the production management system of corrugated board production line to control the production cost, the production efficiency of corrugated board production line can be accurately counted, and the speed of the whole production line can be synchronized. Generally, it can reduce the waste rate of corrugated board by more than 5%, and the amount of starch is also significantly reduced.
① Automatic paper feeder
Automatic paper receiving machine is adopted to avoid unnecessary waste, reduce the downtime and quality problems of corrugated board production line, and ensure stable high production speed and high board quality of the whole production line.
② Tungsten carbide corrugating roller
As the heart of the single-sided machine, the corrugated roller plays a decisive role in the quality of corrugated board, and also has a direct impact on the economic benefits of cattle production. Tungsten carbide corrugating roller is a special technology that uses thermal spraying technology to melt and spray tungsten carbide alloy powder on the tooth surface of corrugated roller to form tungsten carbide coating. Its service life is 3-6 times longer than that of ordinary corrugated roller. In the whole roller running life, the height of the corrugated board is almost unchanged, which ensures the quality of the corrugated board to be stable, reduces the amount of corrugated core paper and glue paste by 2% ~ 8%, and reduces the production of waste products.
③ Paster contact bar
The contact bar of pasting machine is made of many wear-resistant arc-shaped plates connected with springs. The elastic force of the spring always makes the arc-shaped plates fit evenly on the paste roller. Even if the roller is worn and sunken, the spring plate will follow the depression, and the corrugated core paper will be uniformly adhered to the paste roller. In addition, the spring with balanced elasticity can automatically adjust the height according to the thickness of the base paper and the change of the corrugated shape, so that the corrugating height of the corrugated core paper when entering the paste machine and the corrugated height when the corrugated core paper is out of the paste machine after pasting are kept unchanged. The glue amount can be effectively controlled and the quality of the paperboard can be greatly improved.
④ Hot plate contact plate
The hot plate contact plate is used to replace the traditional gravity roller contact heat transfer mode. It is made of special wear-resistant material plates, each piece of plate is equipped with spring with balanced elasticity, so that each piece of plate can fully contact with the hot plate, increase the heating area of paperboard, improve the heat transfer efficiency, so as to improve the speed, ensure the intact corrugated board, strengthen the strength of corrugated board and increase the thickness of corrugated board. The paperboard does not degumm, blister and fit Good, reduce the reject rate.
⑤ Automatic paste making system
Paste making process is the most volatile process in the whole production process and the most critical process affecting the quality of paperboard. The traditional paste formula is single, which is easy to cause inaccurate feeding due to human factors, which makes the quality of adhesive unstable. The automatic paste making system is a typical complex of technology, machinery and automatic control. It can process the formula function, historical data, real-time data, dynamic monitoring function, man-machine dialogue, etc. in the paste making system, the paste quality is stable and controlled, and the production can be realized.
Post time: Mar-31-2021